https://erp360.net/about/Implementing an ERP (Enterprise Resource Planning) system erp for industrial fabrication companies can significantly enhance efficiency, streamline processes, and improve overall management. Here’s a breakdown of key components, features, and considerations for selecting an ERP tailored for this industry.
Table of Contents
ToggleKey Components of ERP for Industrial Fabrication
Inventory Management
- Track raw materials and finished goods.
- Monitor stock levels and automate reordering.
- Manage inventory across multiple locations.
Production Planning and Scheduling
- Plan production schedules based on demand.
- Allocate resources efficiently (machines, labor).
- Monitor production progress and adjust schedules as needed.
Supply Chain Management
- Manage supplier relationships and procurement.
- Track orders and shipments.
- Optimize logistics and distribution networks.
Quality Control
- Implement quality checks at various production stages.
- Maintain compliance with industry standards.
- Track defects and manage corrective actions.
Project Management
- Manage complex projects with multiple stages.
- Track project timelines, costs, and resources.
- Collaborate across teams and departments.
Financial Management
- Manage budgeting, forecasting, and financial reporting.
- Handle accounts payable/receivable.
- Integrate with banking systems for real-time financial data.
Human Resources Management
- Manage employee records, payroll, and benefits.
- Track labor hours and productivity.
- Plan training and development initiatives.
Customer Relationship Management (CRM)
- Manage customer interactions and sales pipelines.
- Track quotes, orders, and customer feedback.
- Analyze customer data for better service and retention.
Data Analytics and Reporting
- Generate reports on various KPIs (Key Performance Indicators).
- Use analytics to forecast trends and make data-driven decisions.
- Custom dashboards for real-time insights.
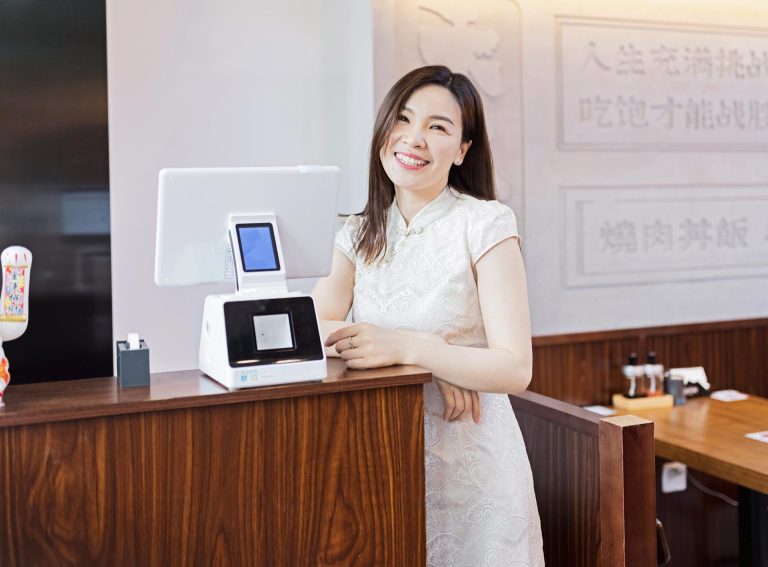
Features to Look for in an ERP System
- Scalability: Ability to grow with your business.
- Customization: Flexibility to tailor features to specific business needs.
- Integration: Seamless integration with existing systems and tools.
- User-Friendly Interface: Easy navigation for employees at all levels.
- Mobile Access: Capability to access the ERP on mobile devices.
- Support and Training: Comprehensive support and training options from the vendor.
Popular ERP Solutions for Industrial Fabrication
SAP Business One
- Comprehensive features tailored for small to mid-sized manufacturers.
- Strong reporting and analytics capabilities.
Oracle NetSuite
- Cloud-based ERP with robust financial management features.
- Integrated CRM and eCommerce capabilities.
Microsoft Dynamics 365
- Flexible and customizable, integrates well with other Microsoft products.
- Good for larger enterprises looking for extensive features.
Infor CloudSuite Industrial (SyteLine)
- Specifically designed for manufacturers with complex operations.
- Offers advanced planning and scheduling tools.
Epicor ERP
- Industry-specific solutions for manufacturing, distribution, and retail.
- Strong production management features.
Implementation Considerations
Define Requirements: Clearly outline what you need from the ERP system based on your specific processes and challenges.
Budgeting: Consider not only the software cost but also implementation, training, and ongoing support.
Vendor Selection: Research and compare vendors, looking for those with experience in the industrial fabrication sector.
Change Management: Prepare your team for the transition. Ensure adequate training and support during the rollout.
Continuous Improvement: Regularly assess the ERP system’s performance and make adjustments as needed to optimize processes.
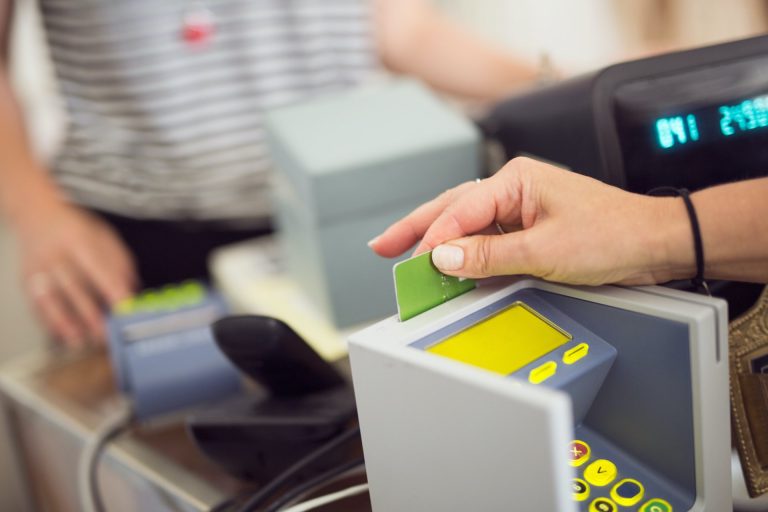
Conclusion
Choosing and implementing an ERP for industrial fabrication companies can lead to significant operational efficiencies, better resource management, and improved decision-making. By understanding your specific needs and thoroughly evaluating potential solutions, you can select an ERP that helps your company thrive in a competitive environment. If you need more detailed information on any specific aspect, feel free to ask!
Steps to Implement Customization
Assess Needs:
- Conduct a thorough analysis of current processes and identify gaps in functionality.
- Gather input from various departments (production, finance, HR) to understand their unique requirements.
Choose the Right ERP System:
- Select an ERP platform that offers flexibility and robust customization capabilities.
- Look for vendors with experience in the fabrication industry.
Work with Experts:
- Collaborate with ERP consultants or developers who specialize in customization.
- Involve key stakeholders in the customization process to ensure their needs are met.
Test Customizations:
- Before full deployment, test customized features in a controlled environment.
- Gather feedback from end-users and make necessary adjustments.
Training and Support:
- Provide comprehensive training to employees on new customized features.
- Ensure ongoing support to address any issues that arise post-implementation.
Monitor and Optimize:
- Continuously assess the effectiveness of customizations and be open to further adjustments as business needs change.
Customization is vital for ERP for industrial fabrication companies to ensure that the software aligns with specific processes, compliance needs, and operational goals. By carefully assessing needs, working with knowledgeable vendors, and continually optimizing the system, fabrication companies can achieve significant improvements in efficiency and productivity.https://abas-erp.com/